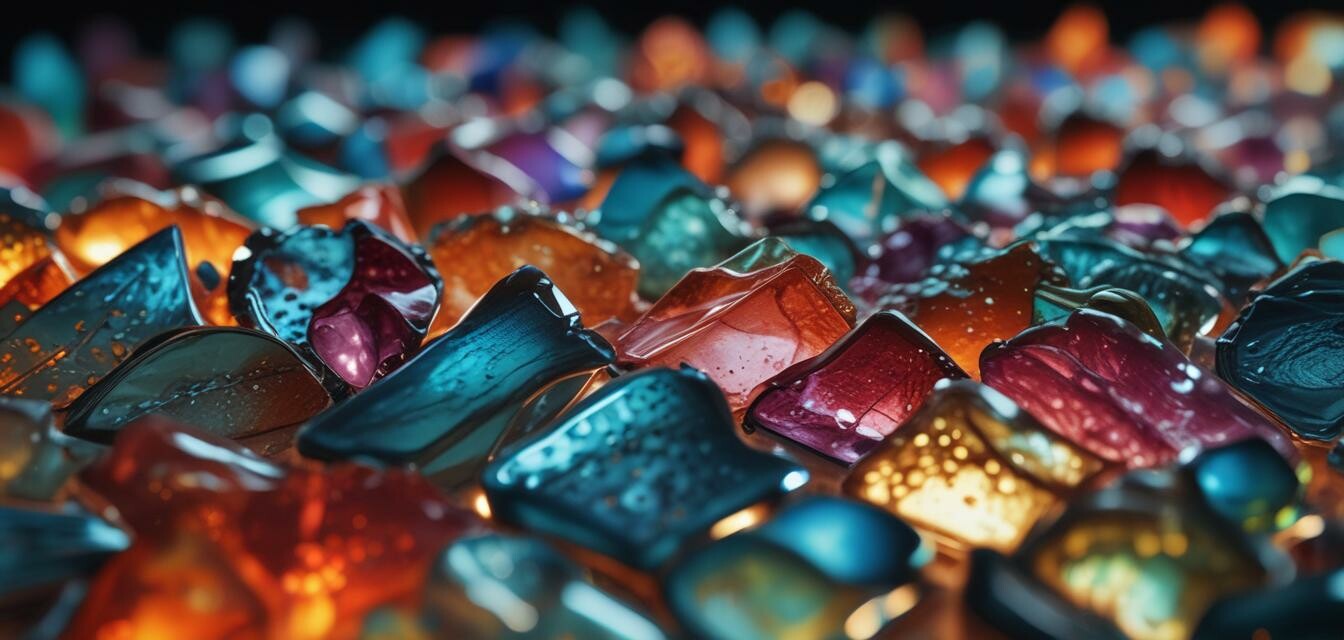
Best Practices for kiln firing schedules
Key Takeaways
- Understand different glass types and their firing requirements.
- Develop tailored firing schedules for specific projects.
- Monitor temperature and time closely to avoid defects.
- Utilize slow cooling to reduce stress in glass pieces.
- Experiment with schedules to achieve unique effects.
Creating effective kiln firing schedules is crucial for achieving the best results in glass making. Whether you're fusing, slumping, or casting glass, understanding the nuances of kiln firing is essential. In this article, we'll explore best practices for developing firing schedules tailored to different types of glass and projects.
What is a kiln firing schedule?
A kiln firing schedule is a detailed plan that outlines the temperatures and durations needed during the firing and cooling processes in your kiln. This schedule varies depending on the type of glass you're using and the specific characteristics you want to achieve in your finished piece.
Key elements of a firing schedule
- Temperature ramp rates
- Hold times at specific temperatures
- Cooling rates
- Glass type (e.g., compatible glass types)
Understanding different glass types
Before creating your firing schedule, it's important to understand the different types of glass and how they behave under heat. Common types include:
Glass Type | Firing Temperature | Common Uses |
---|---|---|
Float Glass | 1300°F - 1400°F | Stained glass windows, decorative pieces |
Fusible Glass | 1300°F - 1500°F | Fused glass art, jewelry making |
Art Glass | 1300°F - 1600°F | Fine art, sculptures |
Glass Ceramics | 1400°F - 1600°F | Tableware, durable glass |
Creating your firing schedule
Now that you understand the different glass types, it’s time to create your firing schedule. Here are steps to help you tailor a schedule:
- Choose your glass type: First, determine the type of glass you'll be using and check the manufacturer's guidelines for firing temperatures and ramp rates.
- Set temperature ramp rates: Gradually increase temperature to avoid thermal shock. A general rule of thumb is to ramp at 200°F/hour.
- Determine hold times: Decide how long to keep the glass at the peak temperature. This varies based on project requirements and glass thickness.
- Plan cooling rates: Slow cooling is crucial for larger pieces to reduce stress and avoid cracking. Adjust cooling rates based on glass thickness.
Sample firing schedule for fusing glass
Here's an example of a firing schedule for fusing glass:
Stage | Temperature | Time | Description |
---|---|---|---|
Heating | 200°F/hr | To 1350°F | Gently bring the glass up to fusing temperature. |
Hold | 1350°F | 15 minutes | Allow glass to fuse together. |
Cooling | 100°F/hr | To 1000°F | Slowly cool to minimize stress. |
Annealing | 1000°F | 1 hour | Further stabilize glass structure. |
Final Cooling | Room Temp | As Needed | Allow to reach room temperature naturally. |
Common challenges and solutions
Even with carefully crafted firing schedules, challenges may arise. Here are some common issues and how to address them:
- Cracking: This can occur if the temperature ramps too quickly. Solution: Slow down your ramp rate and ensure proper hold times.
- Surface bubbles: Bubbles may form if your glass is not properly cleaned. Solution: Clean glass thoroughly before firing.
- Uneven results: This can often be remedied by ensuring consistent heating and cooling throughout the kiln. Solution: Use kiln bricks or shelves to help distribute heat evenly.
Experimentation is key
Every artist's techniques vary, and what works for one project may not work for another. Don’t hesitate to experiment with your firing schedules to find the right balance for your art. Track your results and adjust your methods accordingly.
Conclusion
Creating an effective kiln firing schedule is fundamental to achieving beautiful glass art. By understanding your glass types, determining the right firing parameters, and being willing to test and refine your schedule, you'll be well on your way to mastering your kiln! For more insights, check out our posts on glass kilns and glass molds.
Tips for Beginners
- Always refer to manufacturer specifications for your glass type.
- Keep a journal of your kiln firings to track what works best.
- Start with simple projects to build your confidence.
- Join local glass-making communities for advice and support.
Pros
- Expands creative possibilities in glass art.
- Allows for experimentation and personalization in firing methods.
- Provides a structured approach to complex projects.
Cons
- Requires an upfront investment in kilns and glass.
- Takes time to learn and master firing schedules.
- Mistakes can lead to wasted materials.