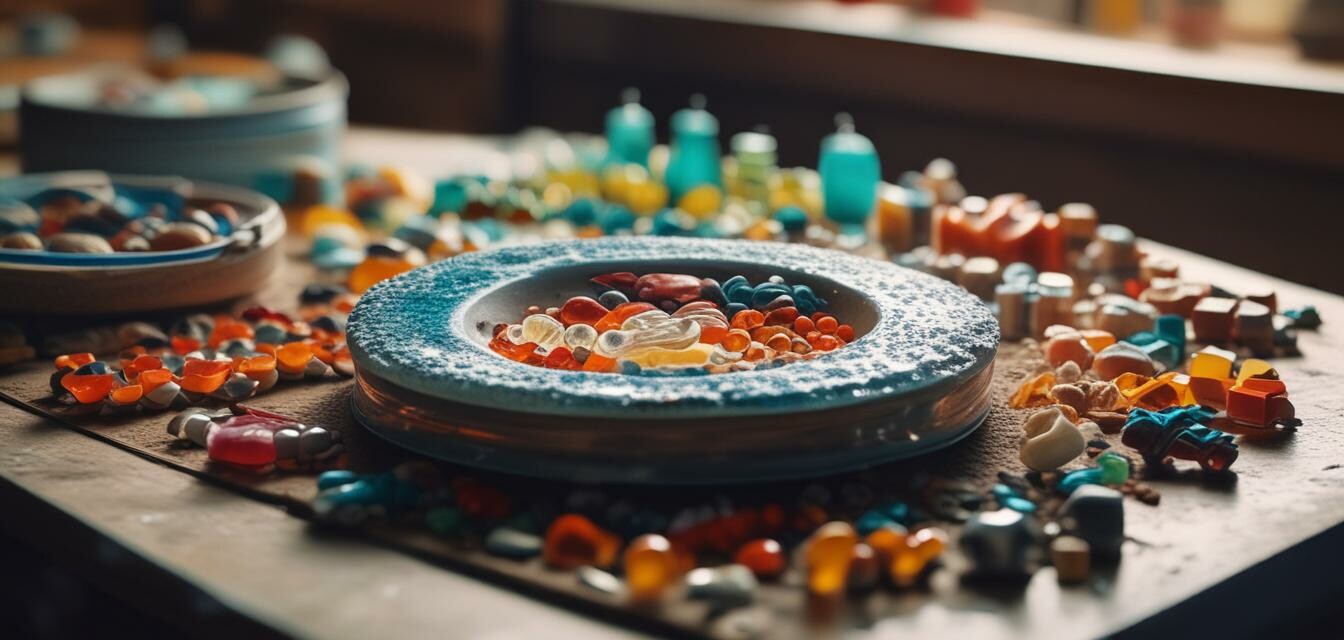
Designing Efficient Firing Schedules for Your Glass Projects
Key Takeaways
- Understand different glass types and their firing needs.
- Establish consistent soak times for optimal results.
- Utilize ramp rates to control temperature changes.
- Adjust schedules based on specific projects and desired outcomes.
- Keep a firing log to improve future projects.
Creating effective firing schedules is critical for achieving the best results in your glass projects. Whether you are fusing, slumping, or casting, understanding how to time your firing process can minimize waste, save energy, and produce stunning glass works. In this article, we’ll dive into how to design efficient firing schedules tailored to your specific projects.
Understanding Glass Types and Their Firing Needs
Before jumping into the scheduling process, it’s essential to know that different glass types have different thermal properties. This affects how they respond to temperature changes during firing.
Glass Type | Recommended Firing Temperature Range (°F) | Key Characteristics |
---|---|---|
Art Glass | 1300 - 1500 | Excellent for fusing, vibrant colors. |
Float Glass | 1450 - 1650 | Strong and versatile, commonly used in windows. |
Fusing Glass | 1300 - 1450 | Specifically designed for fusing projects. |
Stained Glass | 1200 - 1300 | Rich colors, mostly used for decorative windows. |
Essential Components of a Firing Schedule
To master the art of firing, you need to include specific elements that directly impact your glassworking experience:
- Ramp Rate: The speed at which the kiln heats up or cools down, measured in °F per hour. Controlling this helps prevent thermal shock.
- Soak Time: The duration the kiln maintains a certain temperature. This is crucial for fusing glass properly and ensuring it bonds correctly.
- Target Temperature: The peak temperature at which the glass achieves desired results, such as full fusing or slumping.
Creating Your Firing Schedule
The following steps will guide you through designing an efficient firing schedule:
- Identify your project type: Determine whether you are fusing, slumping, or casting.
- Choose the right glass: Select a glass type that matches your project needs.
- Set your ramp rates: Decide on appropriate ramp rates for heating and cooling based on chosen glass.
- Calculate soak times: Adjust soak times according to the thickness and size of your glass pieces.
- Document your process: Maintain a log of the firing schedules that worked best for future reference.
Sample Firing Schedule
For illustration, here’s a sample firing schedule for a glass fusing project:
Stage | Temperature (°F) | Duration |
---|---|---|
Heating | 300 | 30 minutes |
Ramp Up | 1400 | 20 minutes |
Soak | 1400 | 30 minutes |
Cooling Down | 300 | 60 minutes |
Adjusting Based on Feedback
Don’t be afraid to tweak your firing schedules based on the results you achieve. Keep a firing log recording the temperatures, soak times, ramp rates, and any observations on the finished pieces. This will allow you to refine your techniques over time. For more on firing tips, consider checking our blog section on Glass Kilns.
Conclusion
Mastering firing schedules is essential for creating stunning glass art. By understanding the properties of different glass types and incorporating proper techniques, you can maximize productivity in your studio while minimizing mistakes. Remember, each project can teach you something new, so embrace the journey of learning!
Pros
- Helps in achieving desired glass outcomes.
- Prevents defects caused by improper firing.
- Increases efficiency and saves energy.
Cons
- Requires methodical adjustments and may take time to perfect.
- Can be challenging for beginners to grasp fully.
Tips for Beginners
- Start with small projects to test your firing schedules.
- Familiarize yourself with your kiln's manual and its specific firing capabilities.
- Join glassmaking forums or groups for community support and feedback.