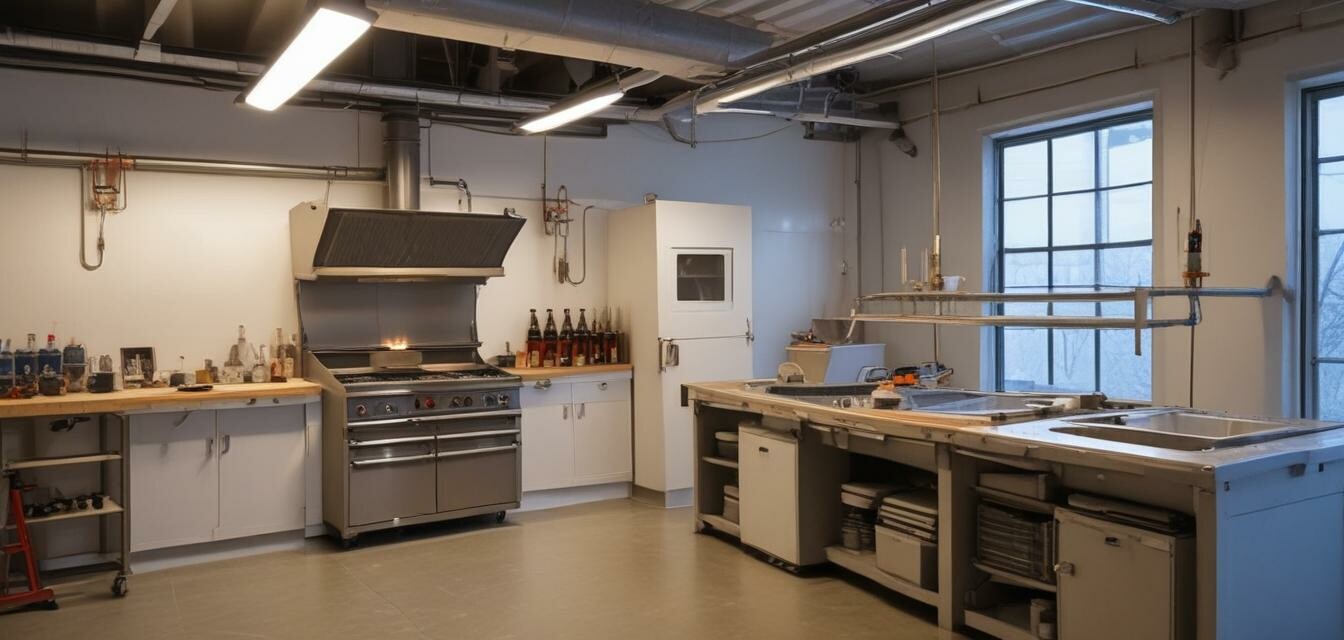
Factors Influencing Kiln Performance
- Temperature control is critical for achieving desired glass outcomes.
- Proper ventilation can significantly affect the quality of the glass and the safety of your workspace.
- Kiln size and insulation impact energy efficiency and firing consistency.
- Regular maintenance is key to ensuring optimal kiln performance.
- Understanding firing schedules is essential for utilizing your kiln effectively.
When it comes to glass-making, the kiln you choose plays a vital role in determining the quality of your finished product. The performance of a kiln can be influenced by various factors, including temperature control, ventilation, kiln size, and maintenance. In this article, we will delve into these essential elements, thus enhancing your understanding of kiln performance and its impact on your glass-making process.
Temperature Control
Temperature control is one of the most critical aspects of kiln performance. Various temperature settings can lead to different outcomes in glass fusing, slumping, or casting. Here’s what you need to consider:
Temperature Range | Glass Type | Common Applications |
---|---|---|
1100°F - 1350°F | Fusing Glass | Combining pieces of glass |
1250°F - 1450°F | Slumping Glass | Shaping glass into molds |
1450°F - 1750°F | Glass Casting | Creating detailed glass art |
With the right temperature control, you can achieve proper melting or softening of glass, allowing for feedback and creativity in your projects.
Ventilation
Proper ventilation in your kiln setup not only helps improve performance but also ensures safety. Here are some aspects to contemplate:
- Good airflow helps reduce the buildup of toxic fumes.
- Ventilation systems can be adjusted based on the firing program.
- A properly ventilated kiln can prevent moisture accumulation, which may affect glass quality.
Types of Ventilation Systems
Different ventilation systems can be integrated into kiln setups:
Ventilation System | Description |
---|---|
Natural Ventilation | Utilizes open windows and doors for air circulation. |
Mechanical Ventilation | Uses fans or blowers to ensure continuous airflow. |
For more details on the types of glass molds that work with your kiln, check out our glass molds category.
Size and Insulation
The size of your kiln directly affects its performance. Here’s how size plays a role:
- A larger kiln allows for bigger projects and potentially more pieces per firing.
- Small tabletop kilns are excellent for beginners or small-scale projects.
- Insulation materials impact the heat retention in your kiln, affecting energy consumption.
Proper insulation ensures your kiln heats evenly and maintains temperatures, improving the quality of your glass art.
Choosing the Right Kiln Size
When selecting a kiln, consider the following factors:
Factor | Small Kiln | Large Kiln |
---|---|---|
Capacity | Good for personal projects | Can accommodate multiple projects |
Energy Consumption | Lower energy costs | Higher but suitable for large outputs |
For more information on kilns and their functions, visit our glass kilns category.
Regular Maintenance
Regular maintenance is essential for ensuring your kiln operates at peak performance. Here are some maintenance tips:
- Check the elements for wear and tear regularly.
- Clean the kiln chamber to avoid contamination between projects.
- Inspect wiring and controls for any issues.
Maintenance Schedule
A suggested maintenance schedule can help keep your kiln in top shape:
- Daily: Check temperature readouts, and inspect the kiln chamber.
- Weekly: Clean the kiln and check for any burning smells.
- Monthly: Inspect electrical components and connections.
Understanding Firing Schedules
Lastly, understanding firing schedules is vital for mastering your kiln. Follow these steps:
- Know your glass type and its ideal firing schedule.
- Adjust schedules based on project requirements, including cooling rates.
- Track your firing results to tweak schedules for better outcomes.
Sample Firing Schedule
A sample firing schedule might look like this:
Stage | Temperature (°F) | Duration |
---|---|---|
Heating | Up to 1300°F | 1 hour |
Soaking | 1300°F | 30 minutes |
Cooling | Under 1000°F | Slow down to avoid cracking |
Pros
- Enhanced glass quality with accurate temperature control.
- Safety improvements through proper ventilation.
- Energy efficiency with good insulation.
- Decrease in project failures with understanding firing schedules.
Cons
- Initial cost for high-quality kilns.
- Ongoing maintenance required.
- Size limitations for small kilns.
By being mindful of these factors, you can optimize your kiln's performance and elevate your glass-making projects. To explore our wide range of glass sheets and supplies, visit our glass sheets and supplies category.
In conclusion, understanding the factors influencing kiln performance, such as temperature control, ventilation, size, and maintenance, will empower you in your glass-making journey. By implementing the best practices outlined in this article, you will be well on your way to creating stunning glass art that reflects your unique style.