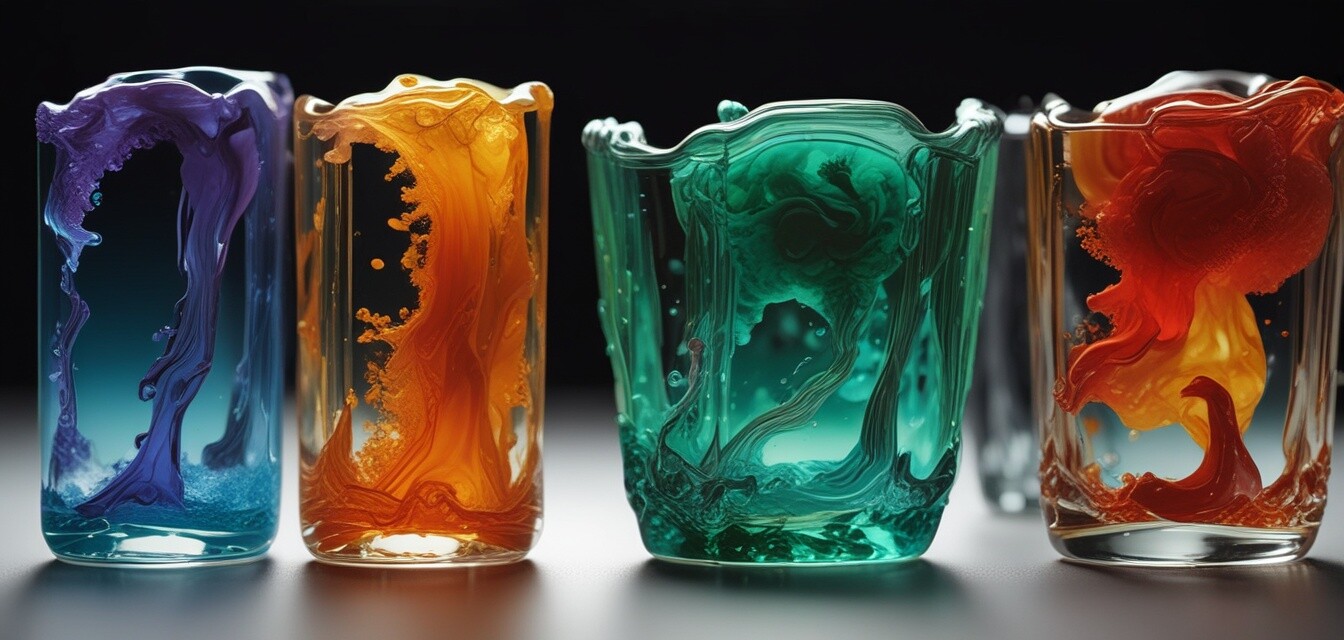
How Different Firing Schedules Affect Glass Quality
Key Takeaways
- Firing schedules influence glass clarity and texture.
- Temperature control is crucial in achieving desired results.
- Cooling rates impact the final piece's durability and aesthetic.
- Experimentation can lead to unique effects and outcomes.
- Understanding your kiln’s characteristics can improve your glass art.
Creating stunning glass art is an intricate dance between creativity and technical precision. One of the most critical aspects that can make or break your piece is your firing schedule. Understanding how different firing schedules affect the quality of your glass art can help you master the art of glassmaking, leading to spectacular results. This article explores the nuances in temperature control and cooling rates, shedding light on how these factors enhance clarity, texture, and overall quality.
What is a firing schedule?
A firing schedule is a detailed plan that outlines the warming, holding, and cooling phases of your kiln operation. It specifies the temperatures and durations that your glass will be subjected to during the firing process. The right firing schedule can enhance the properties of glass, allowing you to achieve your artistic vision.
Key Components of a Firing Schedule
- Ramp Up Time: The time taken to reach the desired temperature.
- Temperature Set Points: The different temperatures at which the kiln holds for specific durations.
- Hold Time: The duration spent at each temperature to achieve specific glass transformations.
- Cooling Rate: The speed at which the kiln cools after the firing cycle.
How Temperature Affects Glass Quality
Temperature is paramount in the glass fusing, slumping, or casting process. Here’s how variations can impact the outcome:
Temperature Range | Effect on Glass Quality |
---|---|
Low Range (around 1300°F) | Often leads to incomplete melting and potential opacity. |
Medium Range (1400°F - 1500°F) | Good for fusing, achieves translucency while maintaining textures. |
High Range (up to 1700°F) | Results in full melting, offers clarity but can warp delicate designs. |
The Importance of Control
Controlling the temperature is critical to achieving precise results. Even a small deviation in temperature can lead to unexpected results. If you are using a kiln with inconsistent heat distribution, regular calibration and experimentation with firing schedules become even more necessary.
Cooling Rates and Their Impact
Cooling rates are equally as important as heating rates when it comes to the final quality of your glasswork. Here is how various cooling rates can affect your projects:
Cooling Rate | Effect on Glass Quality |
---|---|
Fast Cooling | Can lead to thermal shock. Creates more brittle pieces. |
Moderate Cooling | Promotes clarity and reduces stress in the glass. |
Slow Cooling | Allows for more complex textures and enhances durability. |
Utilizing Annealing
Incorporating an annealing phase in your firing schedule is essential for stress relief in glass. This involves holding your piece at a specific temperature, then allowing it to cool slowly. This process significantly enhances the durability of your artwork, making it less susceptible to breakage. To explore more about cooling methods, check out our detailed guide on glass sheets and supplies.
Experimentation: The Key to Unique Effects
The beauty of glassmaking lies in its unpredictability. By experimenting with your firing schedules, you can achieve unique textures and colors that set your work apart. Start by modifying one aspect at a time—be it ramp rates, hold times, or cooling strategies—and document your results for future reference.
Creating a Firing Schedule
Here's a simple template you can use to start crafting your own firing schedule:
Phase | Temperature (°F) | Duration (minutes) |
---|---|---|
Ramp Up | Start | 30 |
Hold | 1450 | 10 |
Ramp Down | Transition | 45 |
Cool | Room Temperature | Until ambient |
Conclusion
Understanding and harnessing the effects of different firing schedules can elevate your glass art to new heights. By acknowledging the crucial role of temperature and cooling rates, and by embracing experimentation, you can unlock new levels of creativity and quality in your projects. Always remember—every kiln has its own set of characteristics, so be sure to spend time familiarizing yourself with your equipment. For further insights discover our categories on glass molds and fusing and slumping supplies to expand your glassmaking journey.
Pros
- Enhances clarity and texture of glass pieces.
- Allows for creative expression through experimentation.
- Helps avoid common issues such as thermal shock.
Cons
- Requires time and patience for optimal results.
- Some experimentation may lead to unexpected failures.