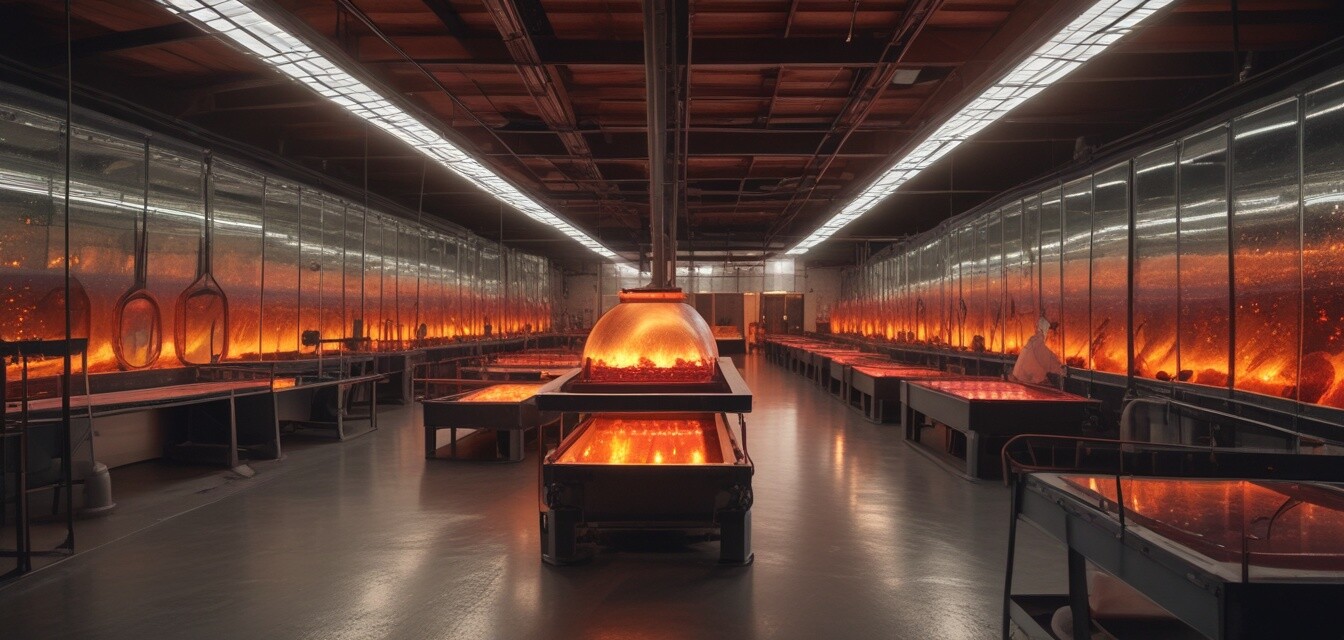
Temperature Zones in Kilns: Understanding Their Importance
Key Takeaways
- Understanding the temperature zones in kilns is crucial for achieving optimal glass firing results.
- There are typically three main temperature zones: the heating zone, the firing zone, and the cooling zone.
- Each zone plays a specific role in how glass transforms during firing and cooling.
- Proper management of these zones helps to prevent defects in glass pieces.
- Knowledge of temperature zones enhances the creative process for glass artists.
When it comes to glass making, understanding the operation of kilns is pivotal for success. Kilns are not just heated boxes; they have sophisticated environments that play a crucial role in the transformation of glass during the firing process. This article will delve into the temperature zones within kilns, how they function, and why recognizing these zones is essential for achieving perfect results in glass firing.
What are temperature zones?
Temperature zones refer to the different areas within a kiln that experience varying temperatures. The efficiency with which these zones work together determines how well the kiln performs, impacting everything from heating to cooling. The proper regulation of these zones can improve the firing process and ultimately lead to better glass results.
The three main temperature zones
In most kilns, especially those used for glass fusing and slumping, you will typically find three main temperature zones:
Zone | Description | Temperature Range (°F) |
---|---|---|
Heating Zone | The area where the kiln initially heats up the contents, gradually increasing the temperature for even distribution. | Room Temperature to 1,200°F |
Firing Zone | The peak area where the glass reaches its melting point, allowing it to fuse or slump as intended. | 1,200°F to 1,600°F |
Cooling Zone | The section where the kiln cools down, allowing the glass to solidify and relieve any thermal stress. | 1,600°F to Room Temperature |
Importance of each temperature zone
Each temperature zone serves a unique and significant role in the glass firing process:
- Heating Zone: This zone ensures the gradual increase in temperature, which is essential for evenly heating glass. Sudden temperature changes can lead to thermal shock.
- Firing Zone: Within this zone, the true magic happens. The glass begins to melt and take shape. Understanding the exact temperatures and duration of this process is crucial for achieving desired finishes and designs.
- Cooling Zone: Cooling is just as important as heating. Proper cooling allows glass to set without developing cracks or imperfections. This gradual process enhances the quality of the finished product.
Common problems and solutions
When artists don't fully understand temperature zones, various issues can arise. Below are some common problems along with potential solutions:
Problem | Potential Cause | Possible Solutions |
---|---|---|
Crazing | Rapid cooling from the firing zone to the cooling zone. | Extend cooling time or use a annealing cycle. |
Incomplete Fusion | Insufficient time in the firing zone. | Increase dwell time at peak temperature. |
Bubbles | Outgassing from glass or trapped air. | Modify heating rates and ensure proper venting. |
Conclusion
Understanding the temperature zones in kilns is vital for any glass artist, whether a beginner or seasoned pro. By mastering these zones, you can ensure better firing results, minimize defects in glass pieces, and elevate your creative process. For more information on kilns and how to maximize their potential, check out our related articles on glass kilns, glass molds, and essential supplies for glass making.
Tips for Beginners
- Familiarize yourself with your kiln’s user manual to understand its specific temperature zones and settings.
- Keep a firing log to record the temperature and time you spend in each zone.
- Experiment with small batches to test different temperature settings and their effects on your art.
- Join online forums or local groups to exchange tips and experiences with other glass artists.
Pros
- A deeper understanding of temperature zones can lead to higher quality glass art.
- Better management of firing processes reduces the possibility of defects.
- Increased creativity as artists explore new techniques without fear of failure.
Cons
- Learning the intricacies of temperature zones can be a challenging process.
- It requires time and practice to perfect the firing techniques related to temperature management.